Clipsham limestone any way you want it from Stamford Stone Company
‘We’re good to go’ says Stamford Stone Company as it gets planning permission for a 37-acre extension to Bidwells Clipsham stone quarry and a new 7,000m2 factory. And it is working to full capacity during the current lockdown.
Stamford Stone Company had experienced the problem of leaving itself short of stone when it took seven years to obtain planning permission for its Medwells Clipsham stone quarry. It did not want to leave itself in that position again as it worked towards planning permission to extend nearby Bidwells quarry, so it has been limiting the supply of block to other stone companies for the past 18 months.
Now planning permission has been achieved to extend the quarry into an area covering 37 acres, which will satisfy demand for the next 30-40 years. With almost 30 years of reserves in Medwells as well, Stamford Stone now feels confident it has enough Clipsham for its own needs and to be able to supply block to other stone companies once again.
Clipsham is won from the company’s two quarries in an area around the Rutland / Lincolnshire border. It is an oolitic limestone, like Portland stone, although it is not quite as well known, probably because Portland has been used so extensively in London ever since Sir Christopher Wren earmarked it for the rebuilding of the capital after the Great Fire of 1666.
In the stone industry, Clipsham is held in a similarly high regard as Portland for its durability, frequently being used for repairs to buildings constructed of less resilient stones as well as for new build.
There is a new display of flooring / paving and walling at Stamford Stone's Helpston headquarters.
Clipsham is currently being used for repairs to the Elizabeth Tower, which is commonly referred to as Big Ben, although that is actually the name of a bell in the clock tower.
Clipsham has also been widely used by the colleges of Oxford and Cambridge, both for repair and renovation work and for new builds, as well as for many mansions and more modest houses from South Yorkshire down to the Cotswolds.
Stamford Stone is currently supplying projects in both Oxford and Cambridge – the redevelopment of the Cambridge Union Society site at Trinity College and a new building at Jesus College, Oxford.
And the stone from Clipsham Bidwells quarry was used for the much acclaimed, award-winning project in Oxford of Bishop Edward King Chapel in 2013, while Clipsham from Medwells quarry was the source of the stone for the Nazrin Shah Centre in 2017, both by Niall McLaughlin Architects.
The entrance to the showroom.
Clipsham Bidwells quarry was then owned by Clipsham Quarry Company (although the stone for the Chapel was worked and supplied by Stamford Stone), and the planning application to extend the quarry had already been embarked upon when Stamford Stone bought the Clipsham Quarry Company in 2018.
Liam Toland of Nottingham planning consultant Heatons deserves credit for his contribution to obtaining the planning permission so quickly, says Stamford Stone Managing Director Daniel Wilson.
Planning permissions involving quarries tend to attract objections and the extension of Clipsham Bidwells was no different. But, as is often the case, objectors can be misinformed. In this case they somehow got the idea that the application included an increase in the tonnage of stone allowed to leave the site, thus increasing traffic movement. But it did not. It had been set at 170,000 tonnes a year previously and the application did not include a proposal to increase that, as was explained by the Directors and Heaton Planning at a public meeting.
It did, however, include a proposal to build a 7,000m2 stone processing plant at the quarry, which is part of the company’s plan to reduce its environmental impact – and would already have been built had it not been for the coronavirus. Because of the uncertainty created by the virus it will now probably be left on hold for a year or so.
Cutting carbon content
Processing the blocks at the quarry rather than transporting them by lorry to the Stamford Stone factory at Helpston, Peterborough, with its CNC saws and workcentre and walling lines will reduce haulage, particularly of the waste that is cut from the block in the production of finished stonework. That waste then has to be returned to the quarry as back-fill.
It is all part of Stamford Stone’s objective of reducing its carbon footprint and minimising its impact on the environment.
Demand for walling stone is as strong as ever.
The new factory will have state of the art processing equipment powered by wind and solar energy. Stamford Stone also plans to plant trees on some of the farmland that was acquired along with Bidwells quarry as part of its commitment to becoming carbon neutral by 2025.
Daniel says: “We hope to set a new benchmark as one of the most ethical and sustainable companies, whose products can be enjoyed for years to come while minimising the impact on the environment.”
With objections to the extension of Bidwells countered and all the Section 106 environmental surveys completed, the final sign off to enable Stamford Stone to start extracting material came in September.
The planning application had been approved, subject to Section 106, in March, just before the country was locked down in response to the Covid-19 pandemic. And Daniel Wilson, with his sister and fellow Director Laura Green, see a positive impact of the lockdown, as it has given them time to catch up with a burgeoning demand and think about their way forward.
One result has been a few new additions to the company. Andy Jeffrey has been recruited as Trade Sales Manager, concentrating on the network of builders merchants the company sells through. Corinna Bolton has been taken on as Sales Administrator, assisting the two sales managers. And Phil Scott has been recruited as Finance Manager, leaving Laura and Daniel more time to devote to overseeing and developing the business.
With half the staff furloughed in the first few weeks of lockdown, Daniel worked in areas of the business he does not usually get involved with in the quarries and factory.
“I saw costs and inefficiencies I hadn’t noticed before,” he says. He also appreciated how much work there was in the two quarries that were being managed by one person and has now given each quarry its own manager.
A human resources company had already been engaged to look after staffing issues, because the number of people employed had grown from 11 to 48 in the past five years. As Daniel says, managing 48 people is different from managing 11, but for a long time he admits he had continued as if he was still managing 11.
It was the same with the computer systems, which have all been renewed this year with the introduction of a CRM (customer relationship management) system to cope better with the size the business has now become. One aspect of the development will involve making Clipsham products available ‘off the peg’ for BIM (building information management), so architects can drop them into their designs.
Of course, lockdown was unsettling when it arrived and created uncertainty throughout the company. Laura: “Of our 48 staff, the 11 office based staff were able to work remotely, and we managed to keep operational with a skeleton staff in the production area and quarries while following strict guidelines. The remaining staff were put on the furlough scheme and, as we found safe ways of working, one by one they were brought back. By the end of July everyone was back full time – which was our primary focus. Redundancies would have been heartbreaking.”
Those who continued to work did not have much problem with social distancing as they tend to be in the cabs of plant or working largely alone in sheds with machines. Only the walling production came to a halt because it requires people to work closer together.
Although a lot of (but not all) housing projects stopped briefly in March and April, many resumed fairly quickly and Stamford Stone found demand for walling quickly outstripping supply. Even now the company is struggling to keep up with demand.
Encouraging cores
Cores drilled on the site of the extension of Bidwells quarry indicate bed heights going up to more than 1m, and tests show the stone is particularly strong and hard wearing, making it ideal for exposed areas such as quoins, cornices and copings. It has being referred to as Davenport-Handley block, after Sir David Davenport-Handley, who owned and worked the quarry for many years before it was inherited by his daughter Sue and her husband, the late Alan Thomas.
As well as the familiar warm colour of Clipsham, Bidwell quarry also produces a lighter coloured Clipsham Cream, currently being used for a private house in Birmingham and another in north London that has what Daniel describes as “some really lovely masonry”. Clipsham White is a particularly hard stone.
To extract the Clipsham, Stamford Stone has Leibherr excavators in each of its quarries and Leibherr and Komatsu loading shovels. It has two Fantini saws on JCB backhoes for squaring up the blocks in the quarries to minimise the waste to be moved and is looking into the idea of wire sawing for the extraction of the stone from Bidwells.
To produce as much product as possible from stone extracted, Stamford has its own Lehman’s crusher and screen, although Daniel says it struggles with the large size of blocks from Bidwells and is a good example of why you should think of the future when investing in equipment.
Daniel did not want to get into aggregate production but Bidwells Quarry has a substantial amount of overburden to be removed before the Clipsham stone is uncovered and that overburden has to be dealt with. At Medwells, the Clipsham is near the surface and can simply be lifted from the quarry face.
It is surprising how different Bidwells and Medwells quarries are, given how close they are to each other. “They are almost polar opposites,” says Daniel. He believes that should mean they work well together with different products coming from each.
Also from Stamford Stone...
Stamford Stone has an associated company to fix stone. Called Stamford Stone Construction and employing 20 stone fixers under the direction of Lee Muxlow, it was set up because some projects, particularly large country house builds, demand supply and fix of stone and Stamford Stone was losing out on the supply when it could not also fix.
And Stamford Stone is involved in the design of projects, with Daniel Wilson commending the skill of his design team. He says they are usually asked to design the stone detail for projects and can often identify ways of making the use of stone more successful and less expensive. The design, supply and build package has proved particularly popular among the growing army of self-builders.
As well as walling stone and masonry, Clipsham is used for flooring, and Daniel has expanded the flooring side of Stamford Stone’s business by adding imported stone. It is displayed in the company’s showroom at Helpston, where Luciana Ciarla has just taken over as Showroom Manager.
Outside, a new display has been created showing a house during construction and encompassing flooring / paving, with a stone pizza oven in the middle. The main aim is to push the paving market.
The showroom now includes a display of Ca Pietra ceramics.
A new line for interiors, added post-lockdown, is Ca Pietra ceramics for walls, the thinking being that if people are buying floors they are quite likely also to want tiles for the walls, and Ca Pietra is a brand that maintains the high quality established by the stone.
For the interiors side of the business, a new e-commerce website is opening soon at stamfordstoneathome.co.uk.
Stamford Stone has not moved into marble and granite worktops and vanities and has no plans to do so. Daniel and Laura think there are already enough companies working in that part of the stone industry.
2020 has certainly been an unusual year for Stamford Stone Company, as for everyone else, but Laura says: “It’s been a year of reflecting and planning for the future. With the rapid growth we’ve been through over the past few years, sometimes we felt as if it was all a bit out of control. Now with both Clipsham quarries having planning in place, a great workforce, robust systems and some exciting projects on order – we’re good to go.”
Bidwells quarry has received planning permission to extend into another 37 acres of Clipsham stone. A 7,000m2 stone processing workshop will be built in the quarry to reduce haulage. It will be powered by renewable energy to further reduce the carbon footprint of the stone.
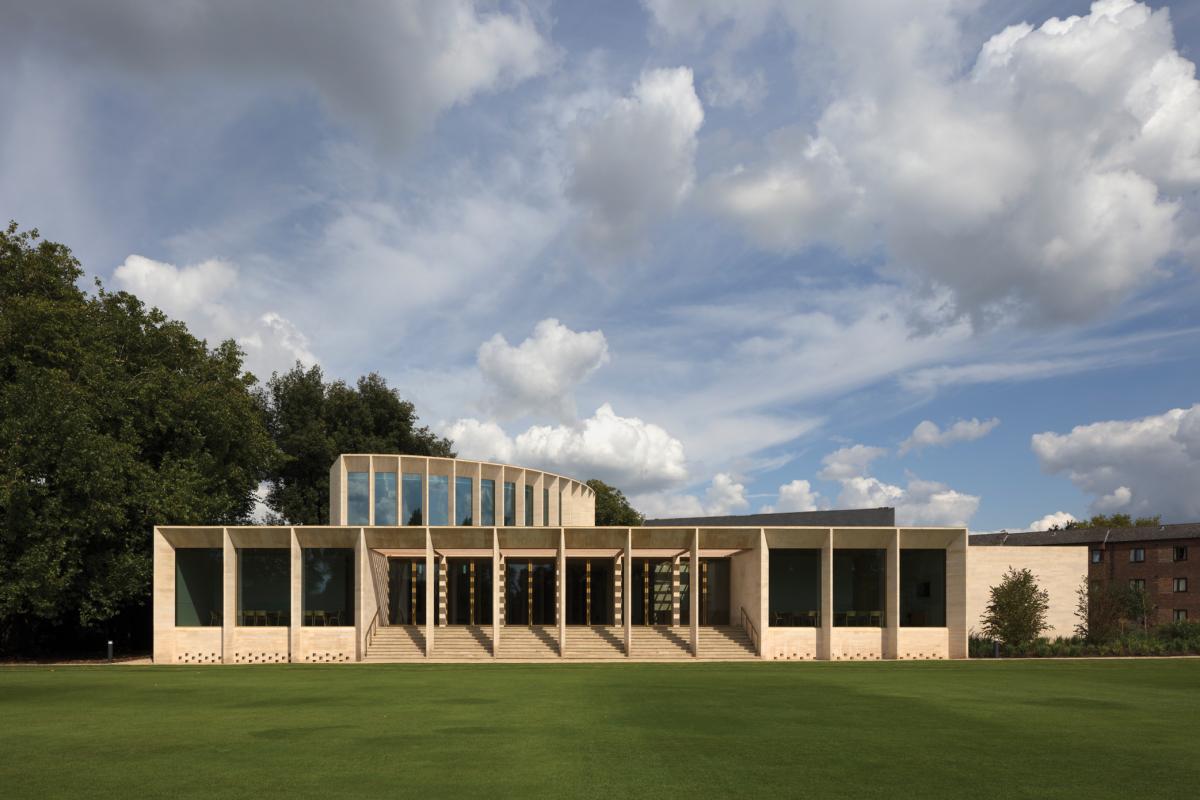
The award-winning Nazrin Shah Centre in Oxford.